Offshore modules, like accommodation modules, office modules, or workshop modules, are often deployed to marine vessels and facilities or remote land locations. These harsh environments require that these modules function correctly to ensure the safety of both the module and the people and equipment they are housing. To ensure that these modules are up to the task, they are taken through a thorough load-out checklist. Then once on location and installed, they are taken through a commissioning checklist to ensure proper installation and that the units are functioning correctly.
As a leader in providing offshore modules to offshore and remote onshore locations, Armoda has developed detailed checklists to ensure that our modules are ready to meet the needs of the project and personnel they are supporting. In this article, we will go over what a load-out checklist consists of, what a commissioning checklist consists of, and the benefits of requiring that these checklists are completed for every project deployed.
Load Out Checklists for Offshore Modules
The load-out checklist can be broken down into three main categories, clean-up from the previous rental, shipping, and certification of the offshore module. Each category contains multiple activities that must be accomplished to check that category off the load-out list.
Clean Up and Inspection of Offshore Modules
When offshore modules are returned from being deployed, they must undergo a thorough cleaning and inspection before being put back into the field. This inspection includes visual assessments of the unit to verify condition and equipment, cleanliness, and separate category-specific check sheets that apply to the unit.
- Unit Cleaned - Vacuumed, mopped, equipment wiped down, trash removed.
- Paint Condition – No visible rust.
- Customer and SSRG Decals Applied
- Doors Functioning / Locate Spare Key
- All End Devices Mounted
- No visible damage to architectural finishes
- Specific Check Sheet (If applicable) - Electrical, Plumbing, HVAC, Zone Cabin
- Shipping
Preparing modules for shipping will ensure they can handle the rough nature of getting the unit to the location. The rough journey will include the ride on the back of a trailer and being lifted with and placed with a crane onsite. Prepping for shipping ensures it is ready to be commissioned at the location. This section of the checklist confirms that all necessary items are secured for transportation, along with the weight and dimension information for lifting.
- Loose items secured or seabraced
- List of shipped loose items
- Sling shipped loose inside, on a separate pallet, or attached to the building.
- List weight: gross, tare, mass
- All bulkheads and panels bolted and secure
- Linen quantity (If applicable)
Certification of Offshore Modules
The certification section covers the necessary information required for the modules depending on the vessel or facility they are being installed on and where in the world it is to be located. This includes items such as DNV certification, PAM (ABS/USCG), and Sling certifications.
- Sling – Vendor Name, Serial Number, Expiration Date / Inspection Date
- DNV 2.7-1 – DNV Number, Date, Stamp Type (V, VN, T)
- PAM – USCG Number, Last Inspection Date
Commissioning Checklist for an Offshore Module
The commission checklist is utilized once the modules are on location and installed. This list walks through the various module systems and varies depending on what type of module is being commissioned. For example, a G4 Series office module would complete a 36-point commissioning list before being approved for work. This list begins with a power-up and moves to a system start to ensure that all the dampers, airflow, and purges are online and working. It then moves into testing the main door and emergency doors. For pressurized modules, the unit is taken through a series of pressure tests; recording pressure ranges as doors are open and closed.
Following the pressure tests, the unit is reset and started up to perform gas detection tests. There are multiple gas detection tests to run, and with each, the module needs to be reset and started back up before running the next test. After the gas detection tests, is an emergency shutdown test to ensure all systems shut down as intended. Then a series of electrical tests are run, checking the lighting, breakers, and sockets installed within the module. The final check-off is verifying the certification nameplate. Once the checklist is completed, it is signed by the installer and customer’s witnesses, and the module is ready to be put to work.
Using these checklists, Armoda ensures our offshore modules are prepared, commissioned, and ready to support the project to which they are deployed. We've also written about how to protect your next project from unforeseen costs with offshore site surveys.
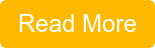